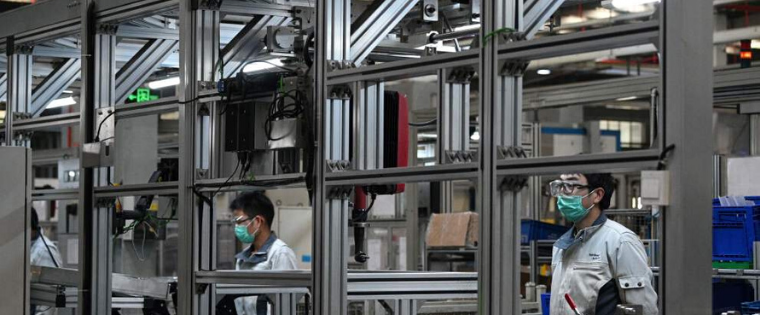
Uncertainty Reigns as Companies Try to Forecast Coronavirus Effects
As Chinese factories slowly return to production in the wake of the Coronavirus outbreak, the question remains how soon will they be churning out products again to meet peak worldwide demand.
Much will hinge the plants’ ability to return to pre-Coronavirus manufacturing levels. Full production for toys and other holiday season-related items typically begins in May. And on top of that, China (which is estimated to account for a little over a third of global apparel exports) is a major production base for sportswear companies such as Puma, Adidas, Nike and others that are hoping for a banner year with European soccer championships and the Tokyo Olympics slated for this summer (and which themselves are surrounded by some uncertainty).
Manufacturing rebounding… slowly
For the most part, many of those releasing earnings last week indicated that manufacturing capacity was slowly increasing in China. Many of the plants were operating at 45-50% of capacity as workers returned. Spin Master said 71% of employees at its suppliers had returned to work, up from 54% two weeks ago. But with many not expected to reach full production until late this month or early April – about four weeks behind schedule – some companies warned of expected declines in Q2 revenue due also to shipping delays from China.
For example, Spin Master projects a “mid-to-high” single digit percentage decline in Q2 sales, while Funko forecasts a mid-single digit decrease and a $15 million impact for the full-year. The companies also demonstrated how delays in China spread outside its borders. About 70% of Funko’s products are manufactured in Vietnam and other countries, yet those plants are reliant on components and tooling produced in China. Nevertheless, Funko projects a 6-9% sales increase this year and expects the impact of production delays to be limited to the first half of the year, CFO Jennifer Fall Jung said.
For Hugo Boss, which sources about 20% of its products from China, the main effects of the outbreak comes from the fact that more than half of its 150 stores in China have been closed since January. The company says the disruption will have a “serious impact” on annual sales in the “low double-digit millions” of dollars.
Meanwhile, several retailers that source products from China appeared less affected by the manufacturing delays. Both Ross Stores and Burlington Stores reported no “material impact”, while Costco CFO Richard Galanti said production capacity at its suppliers in China has increased to 60-80% at some plants, up from 20-30% three weeks ago.
“It’s a slow process, but things are finally starting to get ramped up again,” says Bright Innovations CEO David Bellman. The company expects a six-week delay into May in the first sales of its newly licensed Kathy Ireland GemSpa jewelry cleaning system, the first 2,500 units of which started shipping from South Korea on March 2.
Some shortages
Even with the resumption of full production, many companies expect some product shortages, and are adjusting strategies. Spin Master, for example which ended 2019 with about $180 million in inventory (about 60% higher than it would typically have), will use some of that excess supply to fill in gaps left by late-running goods.
To be sure, the resumption of production in China and accompanying delays are still very much a moving target. But there are increasing signs of stability.