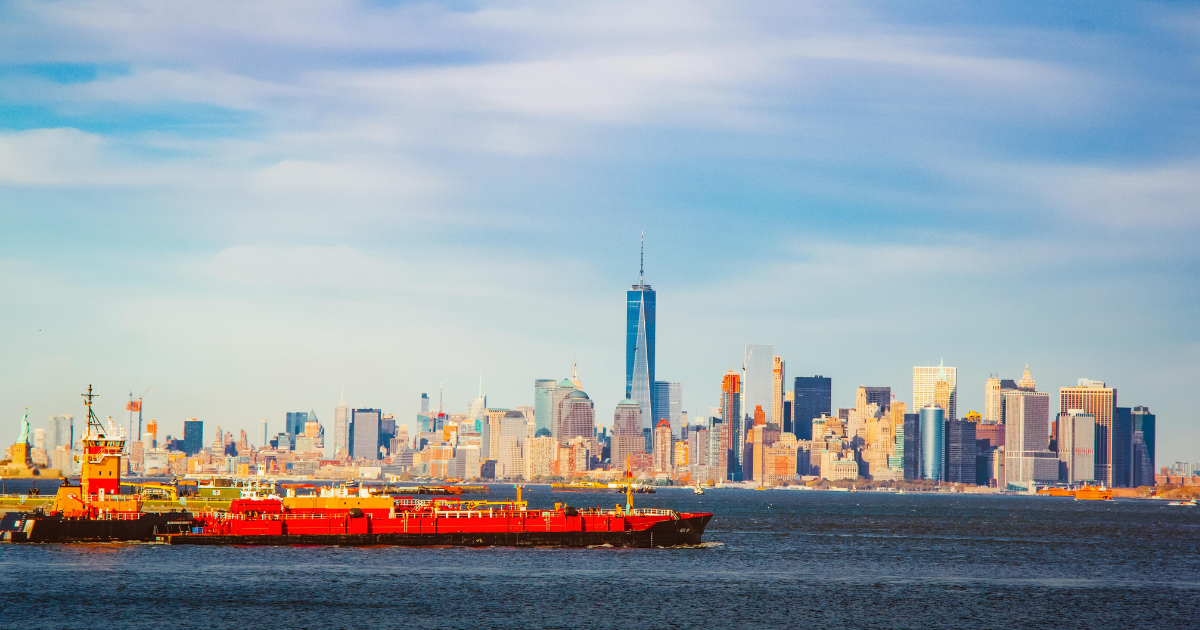
Licensing Industry Navigating Port Strikes
By Mark Seavy
As dockworkers go on strike, the licensing industry is being forced to navigate yet another glitch in the supply chain.
While the strike by 45,000 members of the International Longshoremen’s Association (ILA) halts shipments in ports along the East and Gulf Coasts, the disruption is unlikely to even remotely approach that which clogged ports nationwide three years ago, industry executives said. The East and Gulf ports haven’t suffered strikes since 1977.
To start with, about 70-80% of Q4 inventory has already landed since many retailers and suppliers started receiving and delivering Q4 inventory earlier than usual in late May.
In the toy industry, about 30% of inventory was set for delivery in Q4 and for those products that weren’t specific to holiday business, sales could shift to Q1, said Basic Fun CEO Jay Foreman, whose licenses include those for Care Bears as well as the recent addition of Stretch Armstrong, which will be used for similarly featured Star Wars, DC Comics, Pac Man and other licensed products. A large portion of toy shipments also arrive in ports in Los Angeles and Long Beach, CA, which aren’t affected by the strike.
Licensed beverage and candy in supplier Boston America began receiving Q4 inventory in July, President Matthew Kavet said. But replenishment of out-of-stock items like Elf on the Shelf and Christmas Story candy tins remain outstanding, while new licensed tins for Valentines Day including SpongeBob and Peanuts also could be affected, Kavet said.
Yet the importance of the ports in New York, Newark, NJ, Shreveport, LA, Savannah, GA and others is more critical industries like tableware, said Zrike Brands CEO David Zrike, whose company relies on them for 40% of its shipments. And more than 70% of textile shipments arrive in one or more of those ports, along with perfume (76%) and yarns and fibers (61%).
“The strike will have a huge impact on business for everyone,” said Zrike, whose company has Peanuts and other licenses for tableware. “We have been building up stock in case this happened and thankfully most of our containers have come through. The hope is this doesn’t last long.”
The Biden administration indicated it was unlikely to invoke the Taft Hartly Act, which would force both the ports to remain open and the ILA and the U.S. Maritime Alliance, which represents shipping companies, to the bargaining table.
But economic pressure would likely build the longer the strike lasts. The strike could cost the U.S. economy $4.5 billion to $7.5 billion a week – a hit the gross domestic product that would reverse once the strike is over and shipments resume, according to Oxford Economics.
A one-week strike would stretch congestion at the ports to one month. Costs also will likely rise and whether those increases will pass on to consumers will depend on the length of the strike.
“How pricing is affected and what delays we can expect on our containers arriving in November and December will be predicated on how long this strike lasts,” Kavet said. “While this is an inconvenience for us it will not severely impact our business” for now.
Retailers also have been buying cautiously for much of this year and are unlikely to incur excess inventory as they did in 2022 when they over bought amid fears of coming up short for the holiday season.
“For much of this year retailers were thinking they would rather sell through inventory than carry it over [to 2025] so if there is a little bit of disruption it is going to give manager an excuse for not being fully in stock and everything will sell through,” Foreman said. “If there is any inventory that is late, they will have toys to sell in the first half.”
Any impact of a long strike will likely fall on smaller companies rather than larger ones that have dedicated logistics operations that have been preparing in advance, said Ben Johnston, Chief Operating Officer at small business lender Kapitus. Unlike large retailers, many of whom direct import much of their inventory, smaller competitors likely don’t have the ability to order in bulk and would suffer delays in delivery of critical goods needed for the holiday, Johnson said.
“This strike really highlights the importance of an early start on holiday planning,” said David Charest, Director of Small Business Success at Constant Contact, noting that smaller businesses typically don’t start thinking about the holiday business until October. “Those that have already begun to reach out to customers and ordering inventory are in a stronger position to succeed.”