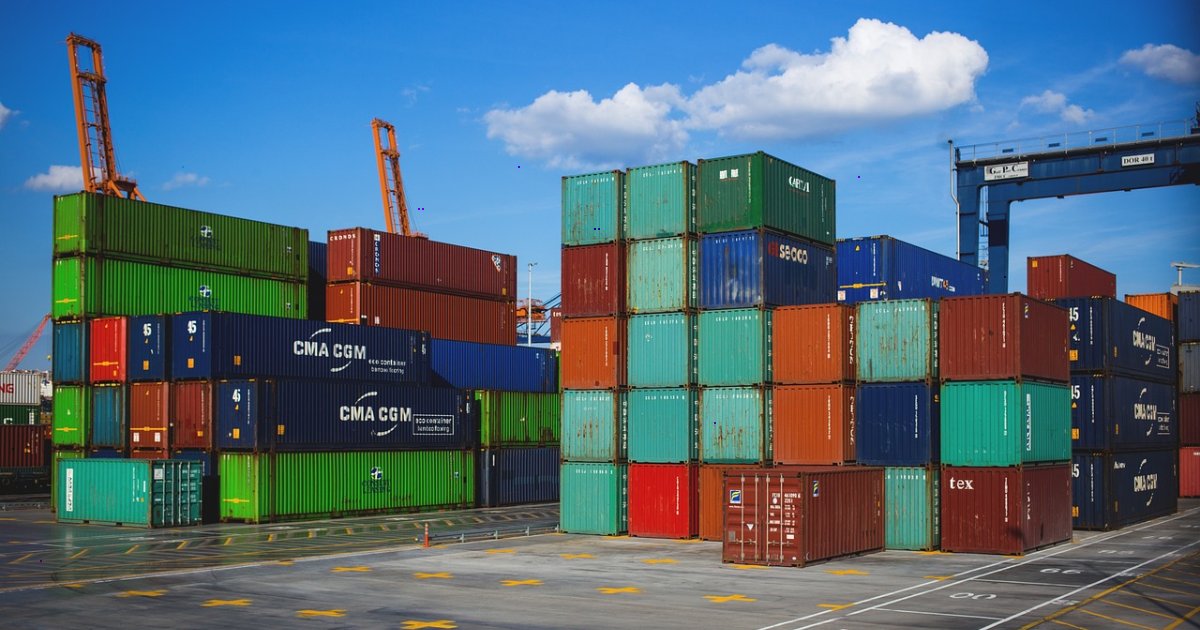
Creating a More Resilient Supply Chain
An Executive Voices Blog by Carmel Giblin, President & CEO of the Ethical Supply Chain Program
As industries evolve and global markets shift, many companies are rethinking their manufacturing strategies. Aside from the immediate concerns faced by all companies given the global tariffs now being implemented for goods entering the U.S., companies have been reviewing their supply chain.
Whether it’s due to the pressure of sustainability, global regulatory requirements, rising costs, or a need for greater flexibility, moving to a new manufacturer or restructuring a supply chain can bring substantial benefits. But with these benefits come challenges that require careful consideration. In working with our members across the globe and from many different industries, the Ethical Supply Chain Program (ESCP) has seen first-hand the key benefits, obstacles, and considerations that companies encounter when looking to adapt their manufacturing strategies in 2025 and beyond.
The Benefits
The most apparent benefit of making a change in manufacturing strategy is the potential for increased efficiency. By selecting a new manufacturer, companies can access more advanced technologies, better production processes, and optimized supply chains. For instance, new manufacturing partners may offer better economies of scale, allowing businesses to reduce costs per unit.
Sustainability is another driving factor. Many manufacturers are investing heavily in eco-friendly practices, renewable energy, and waste reduction programs. By aligning with a partner who shares these values, companies can strengthen their brand’s environmental commitment, which is increasingly important to consumers.
Additionally, finding a more strategically located manufacturer can reduce lead and shipping times, possibly providing relief from tariffs and addressing other issues that create market uncertainty. New partners and a more diversified supplier base can lead to lower costs and improve overall supply chain resilience. In a post-pandemic world, where supply chain disruptions are still frequent, proximity to key markets and strengthening the buyer-supplier relationship has become more critical than ever.
The Obstacles
While the benefits are clear, switching manufacturers or overhauling a supply chain is not without its challenges. The biggest hurdle is often the upfront investment required to transition to a new partner—especially in terms of time, money, and resources. Setting up new relationships, conducting audits, and establishing quality standards can be time-consuming processes.
And those obstacles do not lay solely with the new supplier; a company’s internal team needs to adapt to new manufacturing processes, which may require upskilling or retraining to ensure smooth integration.
For companies short on resources and time, working with a trusted third party that specializes in supplier relations, regulatory compliance, and capacity building can be invaluable in mitigating these obstacles.
Key Considerations
When looking for a new manufacturing partner, several factors should be top of mind. Output capabilities are crucial, and companies must ensure their new manufacturer can handle the required volume and meet production deadlines consistently.
Location is also an important consideration. Proximity to brand owners, retail partners, and end consumers can dramatically influence the overall efficiency of the supply chain. A manufacturer located closer to major distribution hubs can help reduce shipping costs and improve delivery times.
Sustainability programs are important. Environmental and social impacts are concerns for consumers, retailers, licensors, and governments. Companies should consider manufacturers that are actively engaged and committed to responsible manufacturing, respecting both people and the planet.
Finally, businesses should assess a manufacturer’s ability to adhere to specific regulations and quality control standards. Regulatory compliance is key to avoiding fines, production delays, and damage to brand reputation.
Key Regulations
Manufacturing regulations vary significantly across different regions, and companies must familiarize themselves with the local laws before making any moves. For instance, labor laws, intellectual property protections, environmental regulations, and health and safety standards are all areas where compliance is critical.
In the European Union, businesses must adhere to strict environmental and social compliance standards as evident in the proposed CSRD, CSDDD, and ESPR regulations. In the U.S., companies need to be familiar with the UFLPA when importing goods. Similarly, companies must consider the varying levels of regulatory scrutiny and enforcement around labor practices, quality control, and environmental compliance in countries globally.
Companies must also consider the potential costs of tariffs and trade restrictions if they are moving manufacturing to a different region. With the rise of trade tensions, it’s essential to factor in the financial implications of cross-border manufacturing.
Looking Ahead
Several factors will continue to impact manufacturing strategies moving forward. Rising labor costs or labor shortages in certain regions may push companies to look for more affordable alternatives. Ongoing trade tensions, as well as the potential for further pandemics or natural disasters, could disrupt global supply chains and lead businesses to place a higher premium on risk mitigation and redundancy in their strategies.
Sustainability must now be a long-term strategic priority for companies. Business will continue to face increasing pressure from all stakeholders, including both consumers and governments, to adopt more robust ESG practices.
Companies that were once reliant on a single region or country for manufacturing are now looking ahead to diversifying their supply chains to minimize risks. Evolving manufacturing strategies is not just about cutting costs or increasing output—it’s about creating more resilient, flexible, and sustainable supply chains. Companies looking to make a change must weigh the benefits against the obstacles, consider the key factors when selecting a new manufacturer, and stay informed about regulatory changes. As global dynamics continue to shift, adaptive manufacturing strategies will remain critical to staying competitive and meeting consumer demands.
Carmel Giblin, President & CEO of the Ethical Supply Chain Program (ESCP, formerly known as the ICTI Ethical Toy Program), has been with the not-for-profit organization for nearly a decade. She has led the development of the organization and implementation of a range of new services, including supplier assessments and worker well-being programs. She advocates for improved worker conditions globally and is a committed enabler, helping companies to achieve positive impacts through their supply chain operations. For more information, reach out to Carmel Giblin at carmel.giblin@ethicalsupplychain.org.