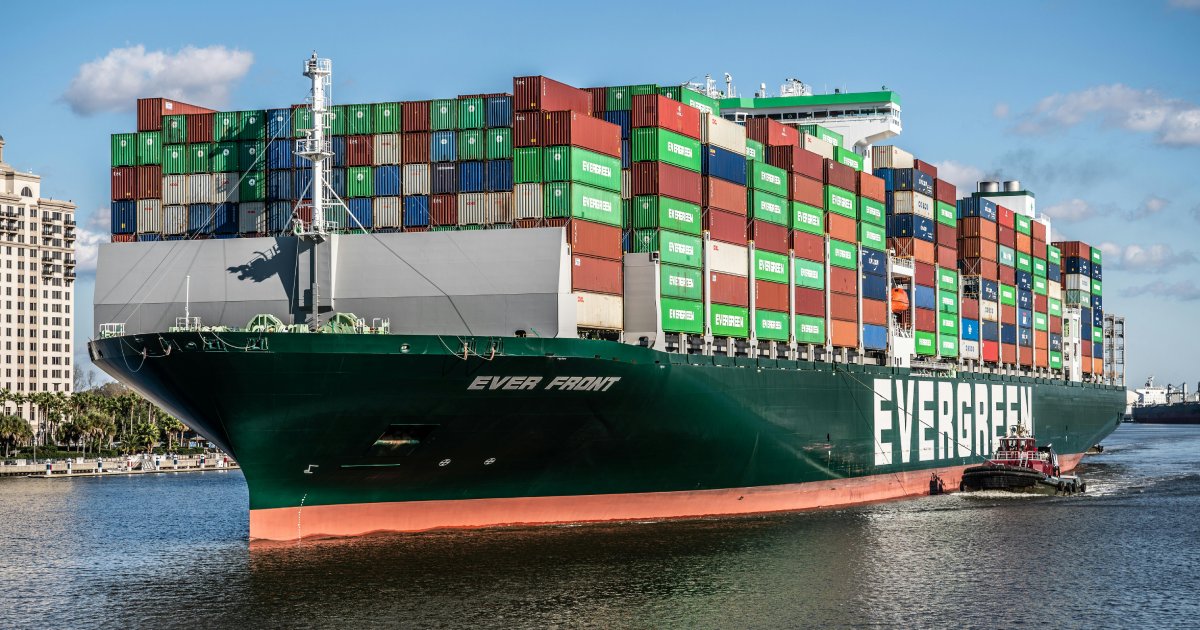
How to Prepare for New Supply Chain Requirements
An Executive Voices Blog by Carmel Giblin, President & CEO of the Ethical Supply Chain Program (ESCP)
A new raft of legislation in Europe will bring an unprecedented level of accountability to companies that license their brand. This means that anyone selling products in the region, no matter where they are headquartered, will soon need to make sure their supply chain oversight and reporting procedures are fully up to scratch.
And North America is following suit, so whether you are a brand owner or a licensee, you need to be ready no matter where you are based. To help you prepare, we’ve laid out what the regulatory changes will mean for the global brand licensing industry and how you can make sure that you stay compliant.
What’s changing?
The European Union is leading the way in its efforts to make manufacturing supply chains both more sustainable and more ethical. In December 2023, an agreement was reached between the European Parliament and Council on the Ecodesign for Sustainable Products Regulation. Once formally adopted, this will require the introduction of Digital Product Passports—containing information about a product’s sustainability throughout its lifecycle—by 2026.
Additionally, a number of measures are being taken to protect the wellbeing of workers. A provisional agreement was reached in Europe in March 2024 to ban any products that have been created using forced labor. This was followed in April by a majority of EU members voting in favor of the Corporate Sustainability Due Diligence Directive (CSDDD), which will require larger companies to ensure that their supply chains do not cause environmental damage or use forced labor. And the Supply Chain Due Diligence Act, which imposes similar responsibilities on companies in Germany, came into force at the beginning of the year.
North America, meanwhile, is not far behind—bills aimed at ending forced labor in global supply chains have already been introduced in both the United States and Canada.
What does this mean for licensing?
Both brand owners and licensees will need to develop greater oversight into how and where any products bearing their intellectual property are being manufactured. It will be essential to meet the specific requirements of each piece of legislation from both an environmental and social viewpoint—simply carrying out an audit will no longer be enough. In terms of the EU’s CSDDD, for example, any suspected use of forced labor at any point in the supply chain must be investigated. If proven, the related products must be removed from the market until such time as the supplier meets the required standard of compliance.
Achieving this will not be easy, particularly for brand owners whose products are manufactured by licensees with a multi-tiered supply chain. To date, too many large companies have relied on the remote auditing of supplier factories rather than delving further into the real problems that exist and trying to fix them.
What is the path forward?
Compliance with environmental and social legislation will require help from experts who are experienced in working with factories around the world and who understand the challenges that may be facing the factory management and workers on the ground. Something as simple as implementing a grievance procedure, for example, can be extremely difficult, and creating a new process in order to tick the right box is pointless unless the local team is able to implement it.
The aim of all this legislation is to bring about real, sustainable change and to improve working conditions for the people who are making products for major brands. When choosing your partner for either area, make sure that it’s an organization whose team is well-established, reputable, and prepared to roll up its sleeves. An effective ESG oversight program should help a supplier understand their responsibilities and take ownership of any improvements needed.
Audit programs should help manufacturers identify areas of weakness in their management systems, remedy any cases of non-compliance, and provide the necessary training and support to eliminate the root causes. This action must be led by brand owners who have the influence to ensure compliance requirements are understood and owned by both the manufacturer and the licensee. And it’s vital that businesses don’t just take their compliance certificate and think the job is done—maintaining standards requires a long-term relationship with understanding and communication on both sides.
This type of legislation may seem far away for many brand owners and licensees, but these requirements will soon be everywhere and investment in your supply chain now could save you significant headache (and costs) in the future. That makes this an investment worth making. When you achieve full compliance, not only will you be protecting your IP, but the whole manufacturing industry will benefit as a result.
Carmel Giblin, President & CEO of the Ethical Supply Chain Program (formerly known as the ICTI Ethical Toy Program), has been with the not-for-profit organization for nearly a decade. She has led the development of the organization and the implementation of a range of new services, including supplier assessments and worker well-being programs. Carmel advocates for improved worker conditions globally and is a committed enabler, helping companies to achieve positive impacts through their supply chain operations. For more information, reach out to Carmel at carmel.giblin@ethicalsupplychain.org.