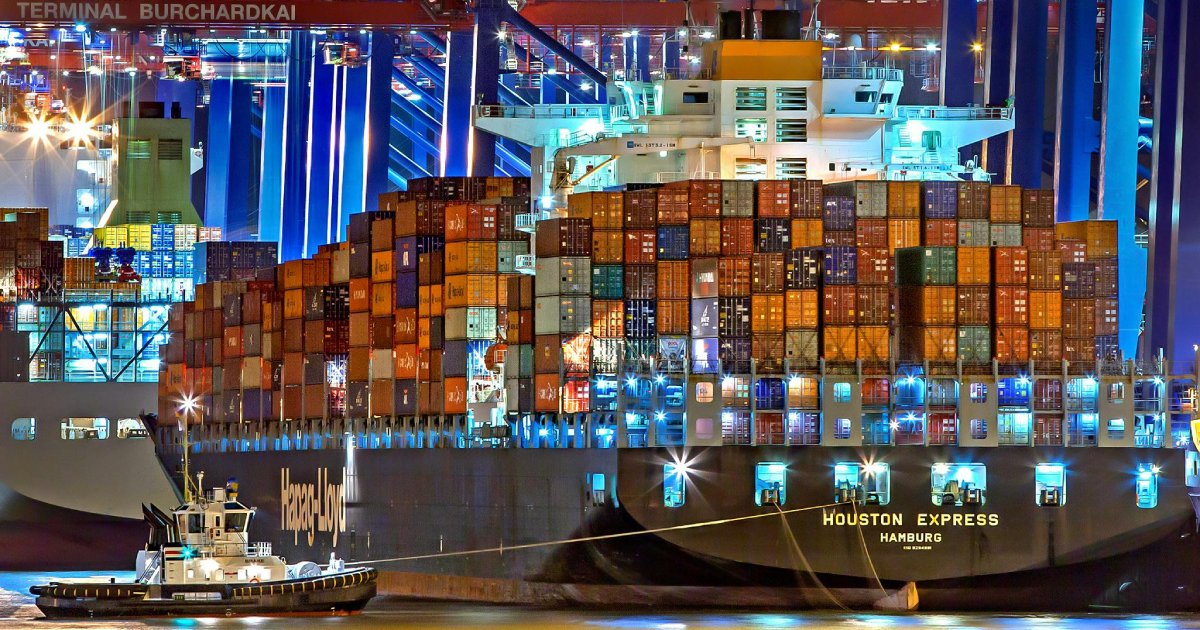
Shipping Delays and Container Prices on the Rise
By Mark Seavy
The shipping delays and cost increases that occurred during the pandemic have returned on a smaller scale, industry executives said.
Shipping container prices sharply declined throughout 2023 but began to rise in mid-November as political unrest affected the Red Sea and the Suez Canal, a crucial route through which 12% of world trade passes. The result has been shipments being re-routed around the Horn of Africa, a shift that has both increased container prices and delayed deliveries by 10-14 days, industry executives said this week at National Retail Federation’s Big Show in New York.
To some extent, the Red Sea shipping route is more critical to Europe than the U.S, but there have been residual effects at ports around the world.
Licensed candy tin and beverage supplier Boston America, for example, has seen 40-foot container prices for shipments from China to the Port of Boston rise to $7,000 from the $2,400 charged a year ago, said Boston America President Matt Kavet. There have been no increases in trucking costs, he said.
Basic Fun, which relies on the Red Sea/Suez Canal route for 15% of its shipments, has seen 40-foot container prices for the European market rise to $4,200 from $1,600 a year ago, CEO Jay Foreman said. The cost of U.S.-bound containers is still at the lower end of the scale and while there have been no issues around capacity, Foreman said.
There have been, however, delays through the Panama Canal, which is suffering from a drought and requires reservations. Indeed, shipping giant Moller-Maersk announced last week it would turn to rail to move cargo as it cut crossings at the Panama Canal due to low water levels causing bottlenecks.
“If we hadn’t been through the supply chain crisis around Covid in 2021 and 2022, the increase would be shocking. But given that [experience], it’s just costly and annoying,” Foreman said. “It adds two to three weeks to shipments and will cause an imbalance of empty containers, which will likely start to be felt in the second half of the year.”
In advance of potential shipping issues, many U.S. ports are making changes to help offset delays or bottlenecks. The ports of Houston and New York are developing plans for 24-hour, seven-days-a-week operation (compared to the current Monday to Friday schedule).
“Those plans, however, will take several years to implement,” said Beth Rooney, Port Director for the Port of Authority of New York and New Jersey.
In the case of Houston, the port authority is working to widen the shipping channel there to 700 feet from 530 feet by September to better accommodate two-way shipping traffic, said Roger Guenther, Executive Director of Port Houston. There also needs to be better sharing of data between the ports and shipping companies, many of whom closely guard customer information, Guenther said.
“We are going to diversify the supply chain so there is redundancy and resiliency that creates reliability,” said Debb Minskey, Trade Lane Manager at furniture retailer Ikea Group, which recently had some Red Sea-bound shipments re-routed around the Horn of Africa. “What shippers want is reliability and consistently so that, if everything is going to be two weeks longer because of the Red Sea situation, you can plan and adjust. It is that uncertainty that is the challenge.”
Ultimately, markets will have to adjust to new norms of volatility with advance planning, said former Party City Chief Operating Officer Peter Smith.
“We now have a couple global wars and supply chain disruption, and it is incumbent on the supply chain to accept the fact that the norm is volatility,” Smith said. “The supply chain must figure out ways to manage, anticipate, and react in a way that is not debilitating.”