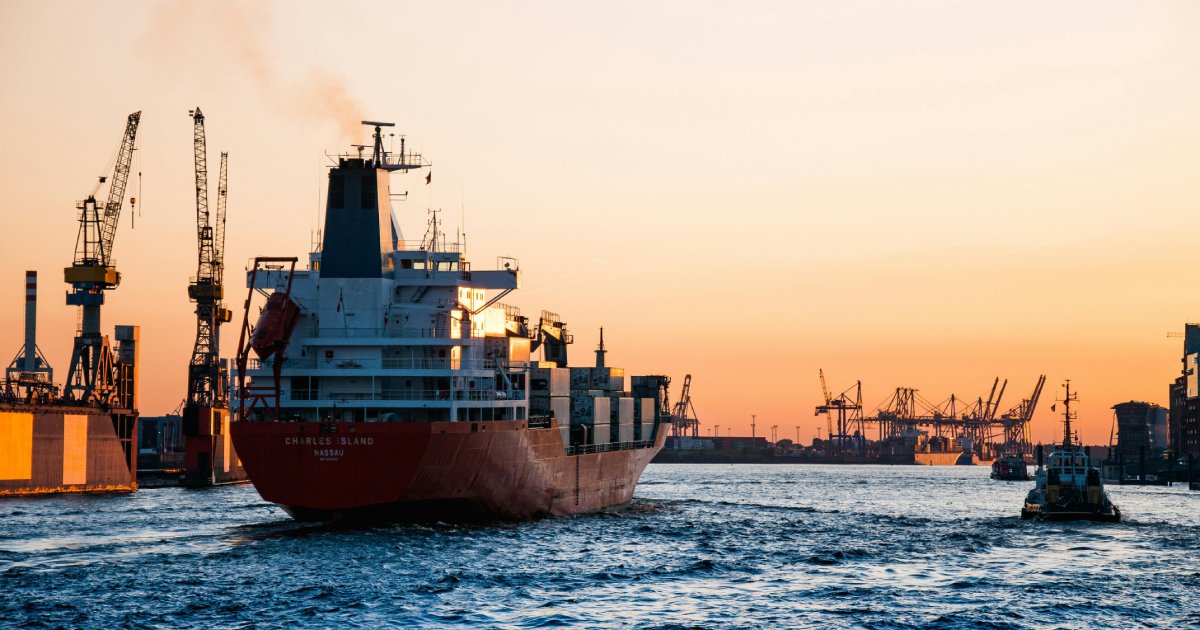
Suppliers Navigate Shipping Issues
By Mark Seavy
While pricing for 40-foot containers appears to be stabilizing after jumping more than 80% in the past three months, concerns about shipping and the supply chain remain.
For example, it’s possible seaport strikes could break out on the East and Gulf coasts where contracts with unionized workers are set to expire on September 30th. Rail union members at Canadian Pacific Kansas City (CPKC) and Canadian National (CN) are expected to go on strike on August 22nd, while members of International Longshore and Warehouse Union Local 514 in Vancouver are still looking for a contract resolution. And there is also continued political unrest in the Red Sea and Suez Canal—a major supply corridor for Europe—which has caused two-week delays as containers are rerouted around the Cape of Good Hope.
“Retailers are concerned by the possibility of a strike at ports on the East and Gulf coasts because contract talks have stalled. Many retailers have taken precautions, including earlier shipping and shifting cargo to West Coast ports,” said Jonathan Gold, VP for Supply Chain and Customs Policy at the National Retail Federation (NRF).
Additionally, shipments from China to North America hit record highs in June as imports were frontloaded from the typical peak in Q3, something that could contribute to “severe congestion and massive spot [shipping] rates,” said Charlie O’Connor, Team Lead for North America at market analytics firm Xeneta.
As a result, retailers are working to get inventories on an earlier schedule than in past years. In fact, Walmart recently launched a cross-border shipping program under which its Marketplace sellers can use its logistics network for shipments from China.
Unlike the shipping crisis in 2021 and 2022, when container ship supply was tight and prices soared to $20,000 or more, companies appear better prepared this time around. Ground Up, which includes Walmart among its top retail accounts, relied on retailers for shipping directly to their warehouses. Other licensees secured shipping contracts in advance as a hedge against rising costs.
But concerns remain as companies prepare for the holiday sales starting in early November. Lifetime Brands—which has licenses for KitchenAid, Farberware, and Dolly Parton—has reported shipping delays.
“We are seeing the impact of the ongoing conflict in the Red Sea as rerouted shipments take longer to reach Europe,” Lifetime Brands CEO Robert Kay said in a conference call with analysts. “While ocean freight costs have been increasing as a result of geopolitical conditions and due to vessel and container availability levels, we think those levels have stabilized and will remain fixed at the higher base for the foreseeable future.”
Minimizing delays is crucial as the company works to meet growing demand. The new Dolly Parton license for home goods is forecast to generate $10 million in sales this year, according to Kay, and discussions with additional customers for 2025 shipments are ongoing.
While some suppliers have been trying to avoid delays by shifting business to air freight, those costs are increasing as well, O’Connor said. The global air spot rate in July was up 20% from a year ago. And freight forwarders that sell air cargo rates reported they had increased 26%, according to O’Connor. At the same time, air carriers have been moving capacity from regions like Latin America to those in Northeast Asia and Europe, where rates and volume are high.
Amid these logistical challenges, many companies are working to diversify their manufacturing and shipping strategies. For example, some companies are reducing their reliance on China for production both to lower costs and as a hedge against any increase in tariffs.
Lifetime Brands is working to have 25% of its spending on goods coming from factories outside China in Southeast Asia, Kay said, and one of Lifetime’s top-selling products (10 million units annually) is now sourced outside China. Lifetime is also in the process of bringing a new plastics manufacturing facility in Mexico to full production. And household goods supplier Newell Brands, once reliant on China for as much as 45% of its products, has lowered that to 15% with a goal of reaching 10% by late 2025, CEO Chris Peterson said.
“At this point, we have evaluated country of origin on all suppliers and are not signing on any new suppliers that do not have existing or defined plans to establish manufacturing capabilities outside of China,” Peterson said.