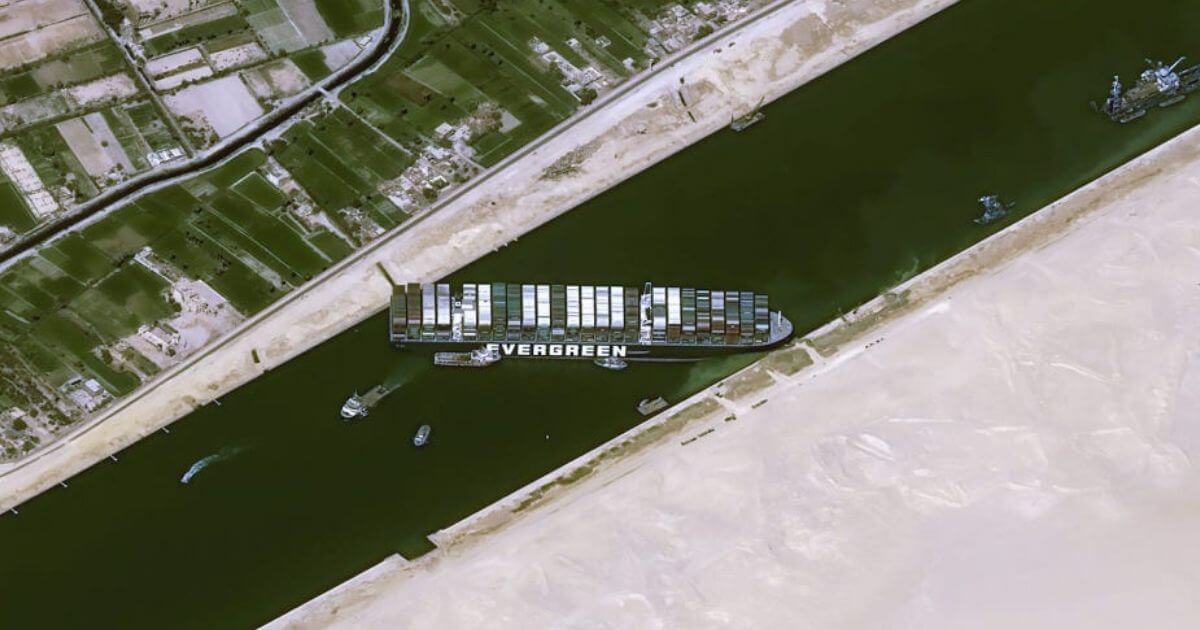
Will Suez Boost Nearshoring?
Has anyone had a worse day than the pilot of the container ship blocking the Suez Canal? (Well, perhaps the companies whose goods are in the containers.) While the ship’s plight has been fodder for plenty of memes and late night comedy, it shines a brighter spotlight on the very serious issue of whether manufacturing can move closer to the markets in which the goods are consumed.
A movement toward so-called nearshoring and reshoring was underway well before the pandemic. But it’s taking on added urgency amid weeks of production and shipping delays tied to the year-long COVID-19 outbreak. A BDO Consulting survey found 24% of 100 manufacturing company CFOs polled plan to relocate production to another country this year.
Cost, Speed and Carbon Footprint
That was especially true when the cost of shipping a 40-foot container from China to North America, for example, more than doubled to $8,000 or more last fall. That has started to settle down, but the memory is likely to linger. Also, shifting of production closer to markets offers a speedier path to retail in countries where one-day delivery to consumers is increasingly the norm. And it potentially reduces carbon footprint, another a key factor as consumers consider sustainability in their buying decisions.
For example, Walmart earlier this month said it would spend $350 billion over the next decade on nearshoring production in the U.S. across six categories – a move that could eliminate 100 million tons of cardon dioxide from its supply chain in the next 10 years, according to Boston Consulting Group. This is far from the first time Walmart, which has long been criticized by labor advocates for driving down prices by pushing manufacturing overseas, has gone down that road; in 1985 it staged a big Buy American effort.
China to Brazil
Many companies were already considering moving production out of China amid the trade war the U.S. waged with China in 2019. In Brazil, Everlast licensee Mega Group International moved production of running shoes and other footwear from China over a two-year period starting in 2018, gradually increasing production in Brazil with contract manufacturer Vectron, says Mega CEO Erick Dachieun Liu.
In addition to a cost savings, the shift also cut lead times by more than half to 45-75 days, he said. Mega also benefitted from an established footwear manufacturing base Brazil, best known for men’s formal and women’s shoes, but also including Mizuno and Under Armour licensee Vulcabras.
“Three decades ago, U.S. producers began manufacturing and sourcing in China for one reason: costs,” Patrick Van den Bossche, a partner at the global manufacturing consulting firm Kearney, said in a report released last year. “The trade war brought a second dimension more fully into the equation―risk―as tariffs and the threat of disrupted China imports prompted companies to weigh surety of supply more fully alongside costs. COVID-19 brought a third dimension more fully into the mix, and arguably to the fore: resilience―the ability to foresee and adapt to unforeseen systemic shocks.”
Bottlenecks
Yet the pandemic only seems to have accelerated companies’ decision-making as they struggle to fill retail orders that often wait outside bottlenecked ports for 2-4 weeks. In some cases, retailers are penalizing suppliers for late orders. A candy company executive said a major retailer cancelled an order and then sought to charge it back at full retail based on lost sales.
“Licensees before the pandemic were moving to do that [shift production] for cost reasons alone and so those that were set up seemed to be in better position when the pandemic hit because they had local manufacturing,” says Margaret Kivett, SVP for Global Licensing at the boxing brand Everlast, which has about 50 licensees. “I think licensees are looking at other options, but when everything clears I am not sure, because at the end of day it is about where can they get the best product at the best price.”
Long-term Process
It remains an open question when everything will “clear,” and nearshoring is a process that takes several years, not several months. In the meantime, manufacturing and shipping costs are expected to remain high into the fall before returning to more normal levels in 2022.
And short-term business imperatives will intervene. For example, a small appliance supplier received a large order from Walmart and had little choice but to pay a premium price for manufacturing in, and shipping from, China.
“The costs keep going up and there is a supply and demand issue,” says an executive at the small appliance supplier. “You have to pay premiums to get a chance and we had a Walmart program and paid whatever it took.”